Last February, just a month or so before the coronavirus pandemic really got going in earnest, Emma Shea received a package at Zero Gravity Craft Brewery in Burlington, Vt. It was from PakTech, the Eugene, Ore., firm that produces the hard plastic, solid-hued 4- and 6-pack carrier handles with which the brewery packages its canned beers. But it wasn’t the handles themselves — it was a bin for customers to drop off used handles for proper recycling.
“We emailed PakTech and they mailed us a blue collection bin and some educational signage within two weeks,” Shea recalls in an emailed exchange with VinePair.
But when it came time to actually recycle the used high-density polyethylene handles Zero Gravity had collected, Shea and her colleagues encountered what you might call the PakTech paradox. Despite the company’s claims that its popular handles are both made from 100 percent recyclable materials and themselves fully recyclable, actually recycling them is often more complicated than that.
“We don’t have a convenient location that accepts PakTech handles for processing,” says Shea. “Currently, the nearest location is in Massachusetts, and they only accept them by the truckload.”
So what happens to the PakTech handles that make it to your local brewery, but not a reprocessor? Across the country at San Diego’s Thorn Beer Company — which has offered small discounts on beer for returned handles for the past couple of years — Anna Brigham has an answer. “Any toppers that we can’t reuse goes into our [waste management company] recycling dumpster and hopefully will get recycled from there,” she tells VinePair.
“Though there’s no way to know what’s happening to it at that point.”
PakTech’s craft brew debut
It’s flummoxing stuff, particularly for breweries that choose PakTech’s popular handles because of their recyclability (not to mention the nearly 500 nationwide that, like Zero Gravity and Thorn, have opted into the company’s pilot handle collection program, launched in 2018.) But before we get into all that, it’s worth taking a quick step back to parse how PakTech can handles found their way into the beer business in the first place.
Beer has been sold in 6-packs since the late 1930s, but it wasn’t until 1960 that an American manufacturer invented those clear plastic rings to replace heavier, more expensive metal, wood, and cardboard carriers. After a 1961 deal with a little St. Louis brewery you may have heard of called Anheuser-Busch, these things quickly became the U.S. beer business’s industry-standard 6-pack carrying solution. But they also became notorious among environmentalists and conservation groups for their negative impact on wildlife: When they wound up in the ocean, as they often did, they reportedly strangled the occasional turtle. “Six-pack rings were hugely controversial ever since I was a kid,” recalls Anne Johnson, vice president of global corporate sustainability at material recovery consultancy Resource Recycling Systems, in a recent phone interview. “They’re one of those first things that really ended up being a plastic pollution problem.”
So when American craft brewing’s second wave picked up steam in the aughts, the eco-conscious, small-bore producers pushing it forward sought packaging that was both better for the environment and more suited to their smaller budgets and outputs. Enter PakTech, which in 2008, partnered with Maui Brewing to develop QuadPak and 6Pak carriers, early versions of the now-ubiquitous handles craft beer drinkers know today.
“We feel that PakTech has met our needs in an environmentally friendly way that is certain to create a buzz,” Maui Brewing founder Garrett Marrero told Packaging World in November of that year. The article mentioned the carriers’ dust-cover tops and their versatility (workers could snap cans into them by hand, staving off the need for expensive automation equipment until volume demanded it) as key differentiators. “It’s been extremely successful so far. We barely are keeping up with orders,” Marrerro added at the time.
Those early PakTech toppers might have been less lethal for marine life, but they were still being made with “virgin” HDPE, or high density polyethylene — that is, new plastic. As the American drinking public became more concerned about the climate crisis, and more attuned to the role plastic (in both its production and afterlife) plays in hastening environmental apocalypse, PakTech tweaked its offering.
“I believe in 2012, we started converting our handles away from virgin resin and towards PCR,” or post-consumer recycled materials, says Keenan Hoar, PakTech’s territory sales manager for the eastern U.S. and Latin America. The company has come a long way since then, he tells VinePair. “Right now, all of our can handles, every one that we produce, is going to be made of that 100 percent PCR material, so it’s 100 percent recycled to start.” PakTech says this shift helps it avoid most of the energy and emissions that go into virgin plastic, and all of the oil. The material itself mostly comes from recycled milk jugs, though recently, PakTech has also experimented with a “full circle” program to recycle old handles directly into new ones. Across its entire portfolio — i.e., its non-beer products — the firm still has a few holdout customers using virgin resin, Hoar says, but “our goal is 100 percent conversion [to PCR], and we’re almost there.”
According to its website, “almost half” of PakTech’s business today is manufacturing can carriers. The plastic for those carriers mostly comes from recycled milk jugs, Hoar says. And it’s apparently been good for business — though it’s hard to say for sure. The company, which is privately held, declined to disclose sales figures or an estimate of the number of can carriers it sold last year, and Hoar told VinePair that because it sells both directly to breweries and distributors, “the actual number [of craft brewers using PakTech handles] is almost impossible to pin down.” But even as growth has slowed in the maturing American craft brewing landscape, and competitors have introduced their own carriers (some recycled plastic, some not), PakTech has found new customers in canned wine, RTDs, and even the cannabis space. (The company recently introduced the PakLock, a child-resistant cover for canned THC drinks.) After a pandemic year during which at-home drinking was at an all-time high, Hoar tells me the company’s carrier business “is still continuing to grow, and at a very good rate.”
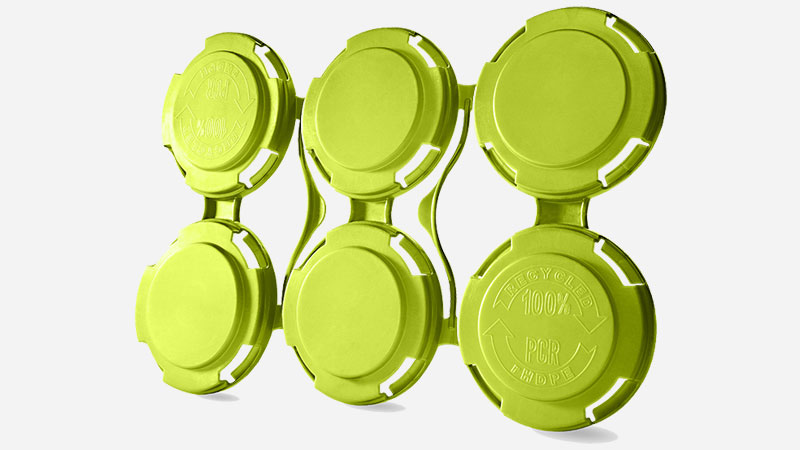
On recycling failures and ‘murph’ misses
But while PakTech’s handles are a popular, cost-effective carrying solution across beverage categories and they create a second-life opportunity for the virgin HDPE #2 material that other companies put into the world, they’re not without downsides.
On the benign end of the spectrum: Rank-and-file drinkers have long complained about the difficulty of breaking beers loose from the plastic toppers. “The cans can be tough to remove from the Pak-Tech when you want to drink one — they’re very secure!” Deschutes’ packaging materials manager Matt Bussmann tells VinePair via email. More troubling: “They are still plastic, which is not as green as other options,” he says.
John Hocevar, the oceans campaign director at Greenpeace USA and the author of a peer-reviewed February 2020 study of plastic recyclability in the U.S., drives this point home: “At the end of the day, if a piece of plastic is floating in the ocean, I don’t really care how much recycled content is in it.”
Whether PakTech’s toppers wind up in the ocean is a function, in part, of whether the American recycling system works as promised. And as you may have heard, it doesn’t really, not these days. It’s a very complicated subject, and there are lots of reasons for its failures, many of which, it won’t shock you to learn, are negative externalities of under-regulated capitalism. But for our purposes, the important takeaway is that when you discard a product — be it a PakTech handle, a water bottle, or an aluminum can — into the recycling, it’s more often than not sent to the landfill anyway.
Recycling rates vary depending on material type, geography, and a bunch of other factors, but in 2018 (the last year for which the Environmental Protection Agency published such figures) the recycling rate for HDPE #2 stood at 8.9 percent — meaning that a little over 90 percent of the type of plastic PakTech uses went unrecycled or uncollected entirely in the U.S. With the advent of China’s National Sword policy in 2018, recycling rates likely got even worse, Hocevar and his colleagues speculate. And the coronavirus pandemic hasn’t helped.
PakTech isn’t responsible for single-handedly fixing the country’s broken recycling system, of course. But its handles don’t exactly make it easier on that system, either. Even if you put your handles into the blue bin in your kitchen, and even if they make it to a material recovery facility — an MRF, or “murph” in the jargon — they may not get properly sorted for reprocessing once they’re there.
“Normally I would say go ahead and put it in your bin, but it looks pretty flat,” says RSS’s Johnson, looking at photos of PakTech handles on the company’s website. “I think that if you put it in your bin, it has a chance of getting through” into a bale of to-be-recycled plastics, known to recycling types as “feedstock.” But because the handles are so slim, they may flow with paper, cardboard, and other two-dimensional items, which creates a potential double-whammy: The plastic doesn’t get recovered, and it may contaminate whatever feedstock with which it’s been improperly sorted.
RRS has not studied PakTech handles specifically, so Johnson emphasizes that this is speculation: “It would need to be tested … I would recommend a material flow test at the given MRF.”
But this is not as straightforward as it may seem. According to Greenpeace’s study, there are 367 MRFs across the United States. Their sorting abilities “vary quite a bit,” says Hocevar, as do the materials they accept. So depending on where you live, even if you religiously put your PakTech handles in that blue household bin, the odds are even slimmer (ahem) that they’ll be reprocessed like more easily scanned, three-dimensional HDPE #2 shapes like bottles and jugs.
“All of the curbside recycling picked up by the city goes to a MRF, so the problem is not that it’s not routed through a MRF,” Sabrina Culyba, editor of Recycle This Pittsburgh, a recycling advocacy group, tells VinePair via email. “But MRFs use sorting equipment and a lot of plastic items won’t make it through the sorting process successfully.” That’s why in Pittsburgh, PakTech handles aren’t currently accepted in curbside recycling at all, she adds.
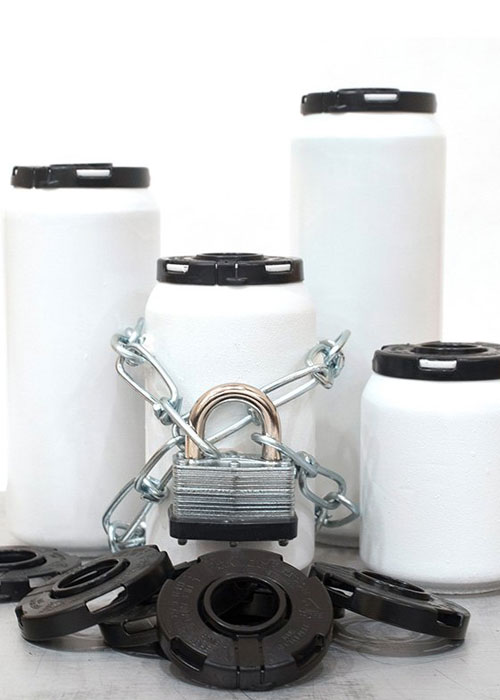
Closing the loop?
None of this is news to PakTech. “It’s difficult for a lot of facilities to recycle these handles,” says Hoar. “It’s been a pretty big frustration on our end.” Which brings us back to the company’s collection program. In 2018, aiming to sidestep the MRF morass and give more of its handles a better shot at actually being recycled, PakTech piloted its own recycling program, partnering with breweries willing to serve as drop-off points for customers’ used toppers.
“We said ‘screw it, let’s build [a system] on our own dime, and see if this works,’” Hoar says. According to PakTech’s marketing materials, there are around 500 breweries currently involved in the program across the country, with another five to 10 coming aboard each week.
The idea is to create a take-back program for PakTech handles that sidesteps the pitfalls of the American recycling system writ large. It operates on the theory that, if drinkers are willing to sort the toppers themselves at home (which many of them are), then bring their personal PakTech stacks back to dedicated checkpoints, that would allow the material to essentially avoid the recycling system and be delivered straight to a reprocessor. And make no mistake, once it gets there, HDPE #2 is very recyclable, and according to Johnson at RRS, has “huge value to American manufacturing.” Because drinkers have already done the hard work of winnowing paper, adhesive, and other contaminants out of their stacks of handles, they’re prime feedstock that reprocessors will pay for by the pound.
“In the best-case scenario [breweries participating in PakTech’s program] can actually sell it back to that plastic recovery facility,” Hoar says. “Not saying that there’s much profit involved, but enough to cover the costs and maintain a third, fourth life for these handles.”
For the breweries, liquor stores, and supermarkets that want to participate, it works just like Shea at Zero Gravity described. They contact PakTech, the firm ships out a bin and some promotional posters (at no cost to the retailer), and customers drop off their handles for recovery. “The process was very easy,” she says.
Will it solve the PakTech paradox? TBD. “There are incredibly successful take-back programs, but usually it’s in a very controlled loop,” says Johnson. Nespresso’s program, for example, yields a higher recycling rate than the national average (which, according to the EPA, clocked a dismal 23.6 percent for all materials in 2018, the most recent year for which that figure is available), but it’s more expensive to run than a curbside program because customers literally mail spent pods back to the company. Barring mail — which works with the small, aluminum espresso capsules in a way that might not for the larger 4- and 6-pack handles— for a take-back program to really work, it must “have the infrastructure to collect from all the potential places it might go,” said Johnson.
PakTech’s program doesn’t meet that mark yet. As a voluntary effort, the drop-off points aren’t evenly dispersed geographically; they tend to cluster in major cities, and are particularly dense in PakTech’s backyard in the Pacific Northwest. “The whole recycling program, we just kind of started it up and it became a beast of its own, so we really rely on communication with customers who say ‘we don’t have this in our area,’” to establish drop-offs, says Hoar. A VinePair analysis of PakTech’s listings shows 10 states have no drop-off locations, while another seven feature just one or two locations for the entire state. Where the drop-off points don’t exist, Hoar hopes customers will encourage their local breweries to inquire with the company to set them up.
“We want this to succeed, and we don’t just want to ship somebody [a bin] knowing that they can’t recycle” the handles they collect, he says. (Maybe not in all cases, though: “Support from PakTech has been minimal,” Brigham says.)
Where they do exist, PakTech’s recovery bins seem popular. “It’s something our customers seem to appreciate,” says Bryan Grigsby, who handles sales and marketing at Oklahoma City’s Elk Valley Brewing Company, which has been a drop-off location since December 2018. “We use it ourselves on a pretty regular basis, as I’m breaking apart 6-packs or making sample packs for an account or something.” (Many breweries and bottle shops repack 4- and 6-packs by hand with recollected handles.) Hoar warns that used handles could cause trouble if fed through automated applicators, but affirms that as long as a handle “looks good,” this type of direct reuse is a viable path. And the handles are sturdy: At East Brother Beer Co. in Richmond, Calif., cofounder Rob Lightner estimates only about 10 percent of the PakTech carriers they take in are broken beyond reuse.
Low-volume hand-packing aside, dropping your handles off at a collection bin may not secure them safe passage to a new life.
In an ideal world, participating breweries return the PakTech feedstock they’ve collected directly to reprocessors. Sometimes, those firms will take delivery of small, inconsistent loads: For example, Deschutes’ Bend, Ore., location sends the handles it recovers to The Broomsmen, a local recycling organization that accepts PakTech drop-offs from individuals, small businesses, and breweries alike. In other markets, those businesses require minimums too high for individual breweries to meet — “by the truckload,” as Shea discovered. (In other markets, Hoar says, neighboring breweries have successfully teamed up to consolidate collections and meet minimums together, something Shea hopes to explore.)
If brewers can’t find a reprocessor to take the handles, or don’t have the space or nearby brewery partners to consolidate collections to meet minimums, then what? Oklahoma City has no commercial recycling program, Grigsby tells me, so when the bin is full, Elk Valley employees bring the recollected toppers home to recycle curbside. If the MRF they wind up at can handle the handles, they’ll be recycled. If not, well, you know the deal. Routing them through the curbside program puts the handles in the same jeopardy as Brigham’s at Thorn, thousands of miles away.
It’s these kinds of inconsistencies, coupled with the fact that much more beer is sold off-premise than through taprooms (particularly in 2020), that drive skepticism of the program’s efficacy for Greenpeace’s Hocevar. “It feels like ‘yes, but,’” he says. “Since so many [6-packs with PakTech handles] are sold in supermarkets, it seems that it’s going to be a really small portion” of customers that actually knows about, much less follows through on, the collection program. As it stands, he continues, “PakTech is producing a huge number of single-use throwaway plastic items that are going to end up in landfills, incinerators, and the environment. We need to be able to do better than that, at this point.”
His suggestion? Calling on your favorite local breweries and asking them to consider other packaging options that don’t involve any plastic, recycled or otherwise. (There are a few, though none nearly as ubiquitous as PakTech, let alone cardboard cartons or old-school plastic rings.) But you may not want to do that, given the costs and logistical challenges associated, not to mention the fact that craft breweries got walloped during the pandemic and are currently in recovery mode, anyway. And depending on your philosophy about recycling — is it a good system worth fixing, or an inherently flawed one designed to provide cover for planet-killing pollution? — you may see PakTech as part of a sustainable solution rather than the plastic problem.
That’s very much how PakTech sees itself. In response to Hocevar’s criticism, the company issued VinePair a written statement from its sustainability officer, Gary Panknin, disputing the notion that the company was profiting off throwaway plastic. ”By utilizing our products it is contributing to keeping plastics out of the environment. In fact, PakTech has currently kept the equivalent of over half a billion milk jugs from being displaced into the environment and eliminated the depletion of resources needed to make new plastic material,” he said. “PakTech handles are not single-use throw away items.”
They certainly shouldn’t be, given HDPE #2’s recyclability. And it must be emphasized again that PakTech is neither responsible for fixing all of recycling’s woes, nor the only company trying to develop a market — in the beer space and beyond — for recycled plastics. But the next time you see a stack of the company’s popular handles, remember: All that plastic has gotta go somewhere, and just because it can be recycled doesn’t automatically mean it will be. “Ideally, we’ll be able to work together as a brewing community, and find a solution that is both environmentally conscious and logistically doable for most,” says Shea at Zero Gravity. For the craft brewing industry, whether such a solution includes PakTech’s recycled plastic handles long-term remains to be seen.
This story is a part of VP Pro, our free platform and newsletter for drinks industry professionals, covering wine, beer, liquor, and beyond. Sign up for VP Pro now!